TRB Lightweight Panels and Structures for the Aerospace Industry
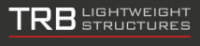

TRB designs and manufactures lightweight panels and structures for the aerospace industry.
Aerospace panels and complete assemblies
TRB manufactures specialised sandwich panels, which can be used for applications where lightweight, stiff panels are required.
TRB combines facing and core skins and bonds them with a high-quality adhesive.
This range includes the cellite 840 phenolic faced, nomex, honeycomb sandwich panel, which is a specially engineered panel for space application.
TRB also offers lightweight storage compartments for first and business class seating in the Airbus A318, cabin crew rest areas for long distance service flights and flight simulators.
Autoclave-manufactured components
TRB also has extensive in-house capabilities, which includes an autoclave system to manufacture high-performance composite components. The vessel is designed and manufactured to meet the requirements of PD 5500, it is 3m in length and has a process mass of up to 500kg, as well as a design pressure of 10bar at 250°C.
The autoclave system compliments TRB’s existing range of machines for composite manufacture that include ovens, computer-controlled, multi-daylight heated platen presses for high-performance material bonding and a 4,000ft² ISO 14644 class clean room.
TRB Lightweight Structures also holds AS9100 (BS EN 9100) accreditation along with ISO 9001. S9100 is the industry-recognised standard of quality and risk management for the aerospace and defence industry aimed at improving service standards and product reliability, which is supported by the world’s leading aerospace companies and supply chains.
About TRB
Established in 1952, its founder George Newell already had more than a decade of experience working with innovative materials in the construction of aircraft. He helped to pioneer the implementation of wooden sandwich construction with a balsa core, which was used to build several well-known aeroplanes. During this time, he experimented with flax-based prepreg, something still in use today, and he co-developed an adhesive called Redux®.
Redux® fundamentally changed the aerospace industry, allowing wing and fuselage panels to be stronger and lighter than a riveted structure. It also made possible early composite structures, joining aluminium to wood.
TRB Participate In Meeting Carbon Neutrality By 2020
The aerospace industry has committed to being carbon neutral by 2020. As such an estimated $1.3tr will be spent on 12,000 new aircraft to meet the target of saving 2.2 billion tonnes of CO2 emissions by 2020.
Recently applying for funding to co-develop a revolutionary panel that will eliminate carcinogens from the production of aerospace grade panels, TRB hopes to manufacture a product that participates in the aerospace industry meeting its target of carbon neutrality by 2020.
With extensive in-house capabilities, industry knowledge and a clear understanding of the challenges faced by aircraft manufacturers, TRB are in an ideal position to service the growing demands of the aerospace industry.
Products and Services
Video
Related Projects
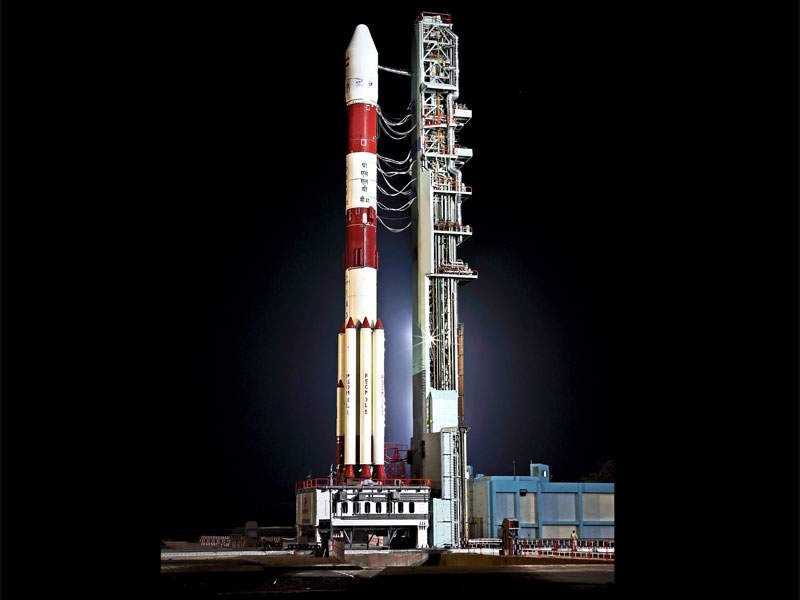
IRNSS-1I Navigation Satellite
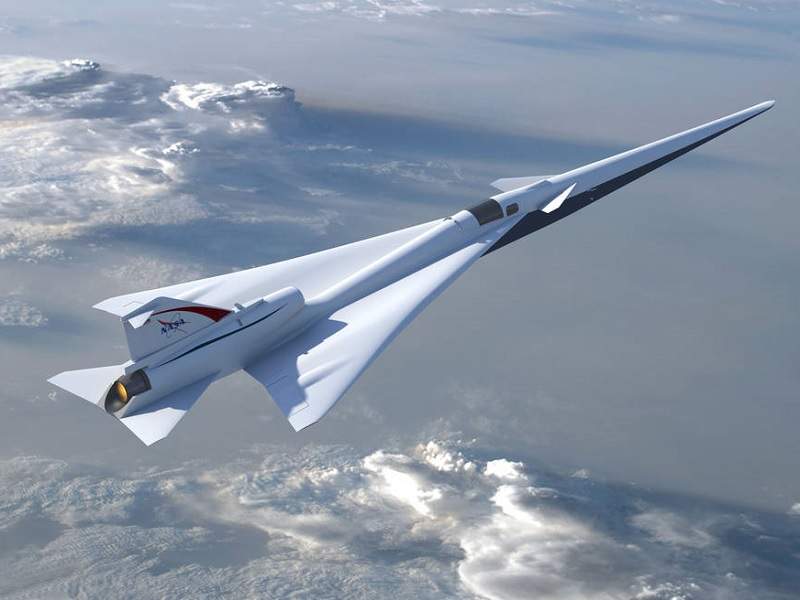
Quiet Supersonic Technology (QueSST) X-Plane

Airbus Beluga XL Transport Aircraft
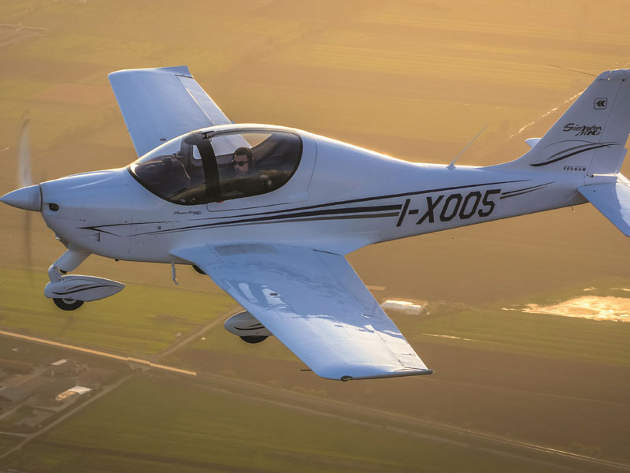
Tecnam P2002 Sierra MkII Aircraft
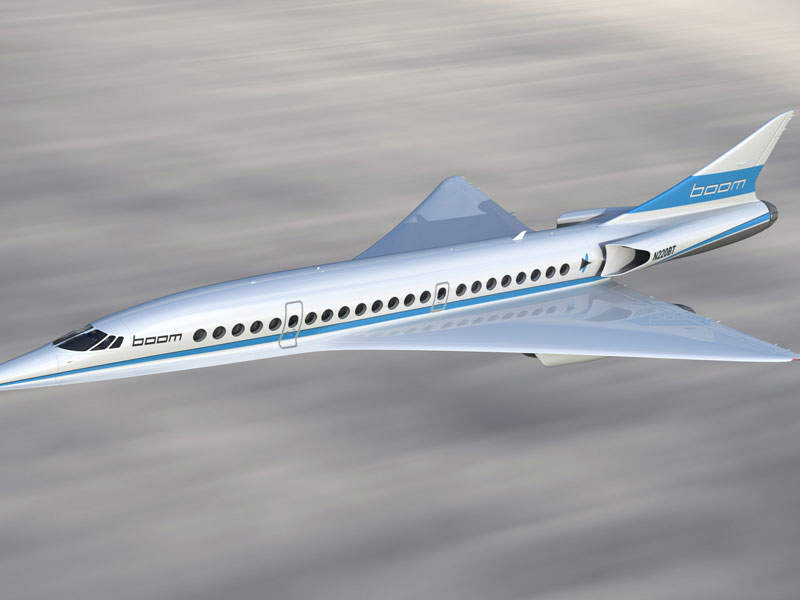
XB-1 Supersonic Demonstrator
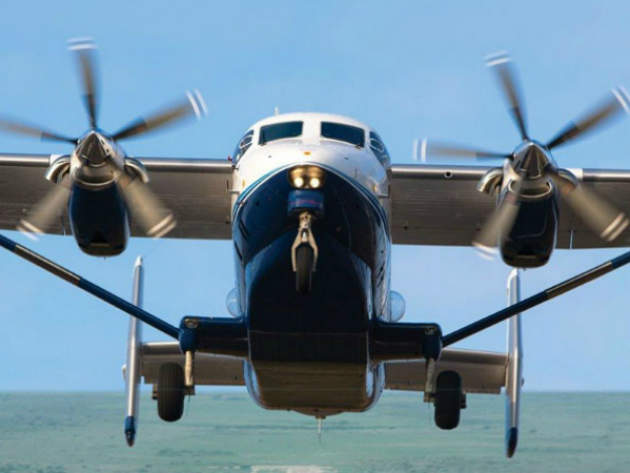
M-28 Twin Turboprop Aircraft
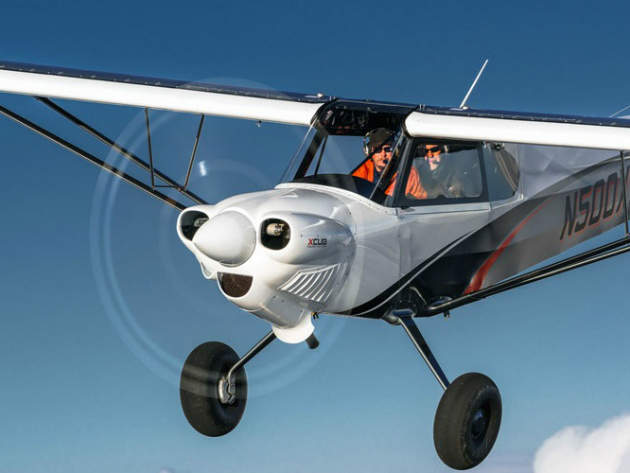
XCub Sport Utility Aircraft
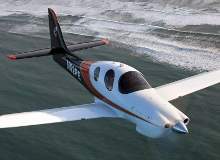
Evolution Piston Aircraft
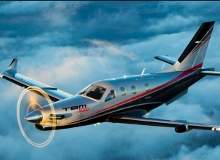
TBM 930 Business Jet
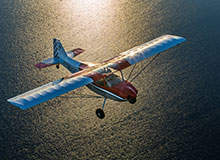
Rans S-20LS Raven Light Sport Aircraft
Press Release
The Covid-19 pandemic has rapidly spread worldwide, affecting the lives of billions of people and having a negative impact on many industries.
Read moreThe value of the global composites manufacturing market is set to skyrocket, particularly as demand for clean transportation continues to increase.
Read moreTRB Lightweight Structures and Toyota Tsusho America have entered a joint venture providing high volume composite parts for the North American automotive industry.
Read moreTRB Lightweight Structures has partnered with international high technology company Safran to develop luxury Skyroom suites for Singapore Airlines.
Read moreRegional Offices
12 Clifton Road
Huntingdon
Cambridgeshire
PE29 7EN
United Kingdom